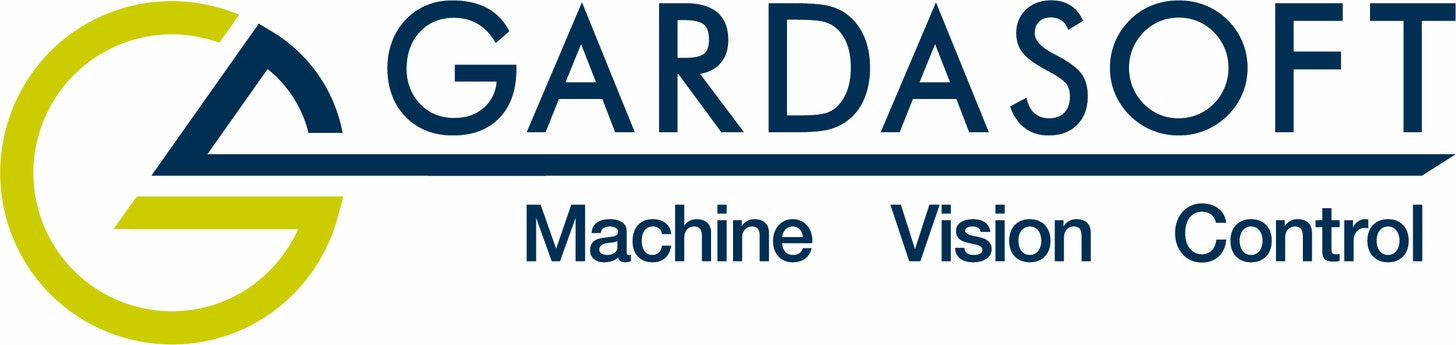
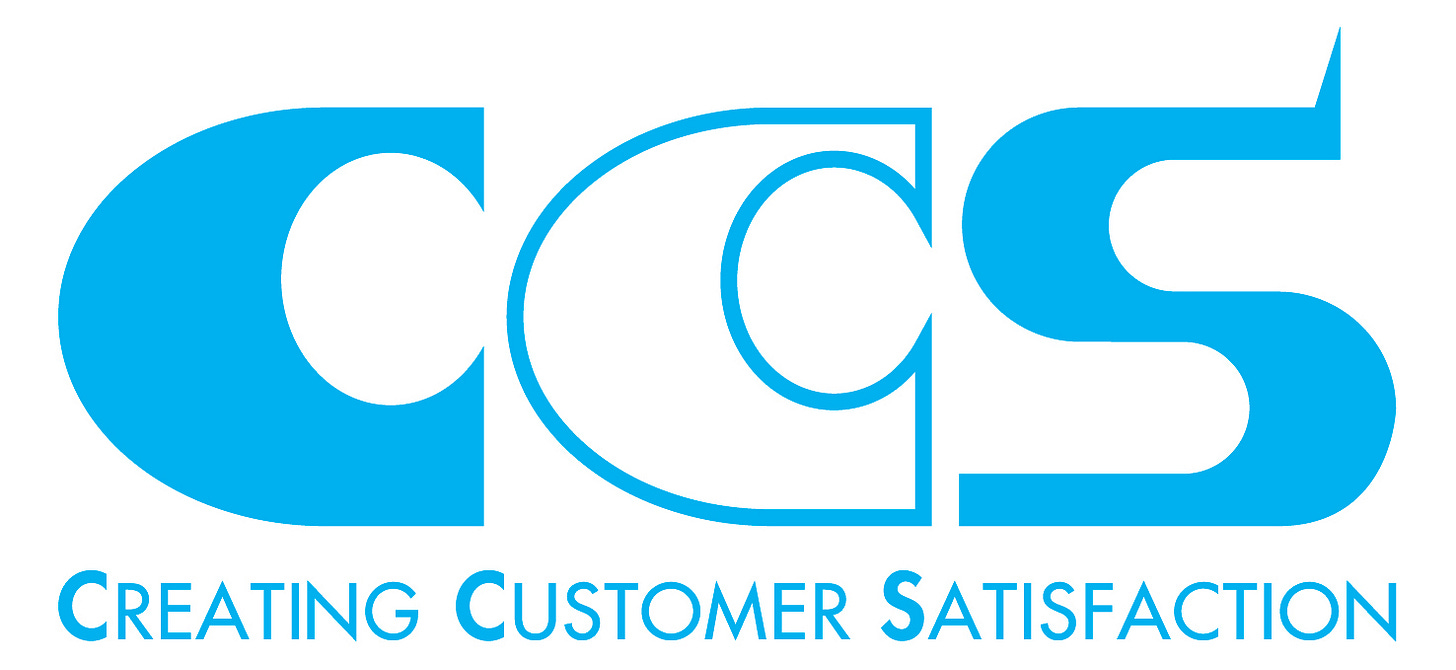
In this feature, courtesy of our Solutions Partner, Gardasoft Vision, we will explain how the different kinds of lighting controllers work in machine vision and which applications they suit best.
First, we’ll cover a few basics about machine vision lighting and the importance of lighting control in getting the best out of a machine vision system.
At the heart of all machine vision systems is a camera which produces the images we need. Not surprisingly, these images need to be of good enough quality for all the subsequent processing and measurements made by the software. This means we need to get enough light from the target object into the camera to give us images with good contrast and with as little noise as possible.
We use LED lighting in most machine vision applications. This needs to provide enough light for the images that we need, but the light intensity must also be consistent from image to image so we don’t introduce unwanted variations in the accuracy of our inspections. But it doesn’t stop there. Many vision systems operate at high speed so we might need to strobe the lights to effectively freeze the motion. Pulsing the light also prolongs the LED lifetime (which degrades with on-time). We might also need to be able to extract extra intensity from the LED for short periods of time. And finally, we need to have the flexibility to be able to adapt the lighting output if the needs of the application change.

So accurate lighting control is a really critical component of a machine vision system. But before we look at the different types of controllers that are available, we need to understand that the crucial factor in LED operation is that the light output is directly proportional to the current flowing through the LED. There are two approaches to lighting control – one based on controlling the voltage applied and one based on controlling the current.
Let’s start by taking a look at basic voltage-based lighting controllers. These are the simplest and cheapest options. However the relationship between the voltage applied to an LED and the current flowing through it is far from linear so even a small change in voltage can produce a large change in current, which in turn leads to a large change in light output. This makes it difficult to control intensity using voltage and these controllers are generally used in applications where the machine vision lighting needs to be on at a fixed level the whole time.
The next step up is the Pulse Width Modulated voltage controller, which offers more flexibility. It provides some degree of intensity control by pulsing the voltage to the LED at high speed so that the average light output intensity is approximately what’s needed. Increasing the pulse length increases the output brightness, but limitations on the cycle speed mean that the intensity control is quite coarse. Not only that, the high-speed voltage pulses can cause EMC interference in neighboring systems. This average light output can also be pulsed using an external trigger for high speed imaging applications but because it can be difficult to generate sharp pulse shapes, the light intensity is likely to vary between exposures.
Current-based controllers, however, provide a much more flexible solution through accurate control of the current flowing through the LED for direct and fine adjustment of lighting levels. They are suitable for all types of requirements from continuous lighting to high speed strobing applications. Pulsing performance is excellent because they can produce consistent and repeatable square light pulses with rapid rising and falling edges. Most importantly, they can also readily be used to deliver another really important machine vision function which is known as “overdriving.” Here the controller can adjust the current through the LED in short pulses to more than its maximum rating to produce much brighter lighting than the maximum specified for the LED. This is incredibly useful in applications requiring short camera exposures. Equally important is the fact that the current controller can automatically control these overdrive parameters to prevent the LED from damage due to overheating. Overdriving is much more difficult to achieve using Pulse Width Modulated voltage controllers.

This has been a brief overview of the different types of lighting controllers that are available. When choosing lighting control for your machine vision system, there are many factors to consider, including budget, speed of the application and whether you need flexibility for future change or expansion. If you really want to get the most out of your LED lighting, current drive controllers offer the most reliability and flexibility – and they’re usually the best choice for all but the simplest systems.
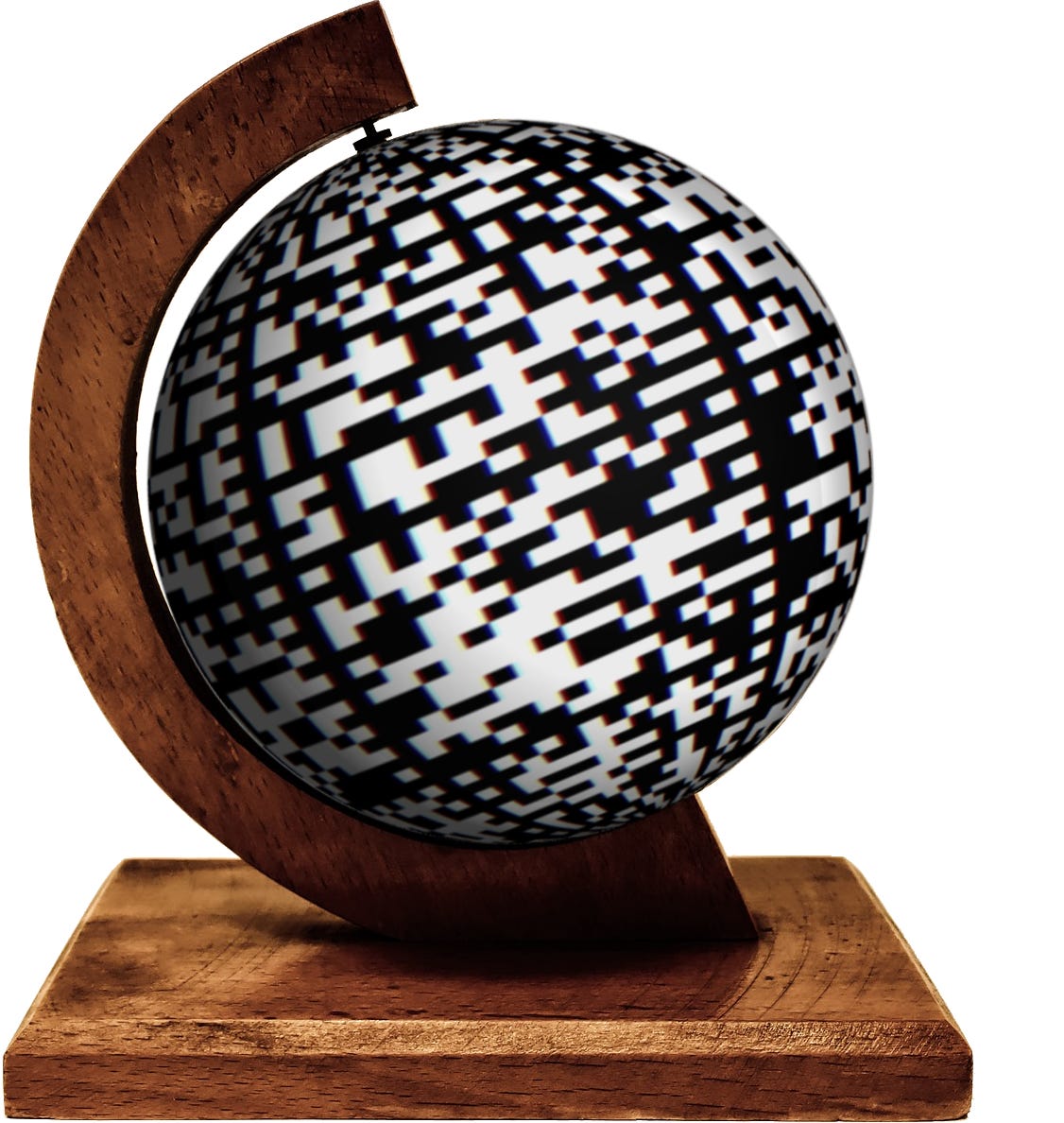
Global Automation & Identification Group thanks Gardasoft Vision for contributing this feature. To learn more about Gardasoft Vision, visit GlobalAutoID.com/Gardasoft
For more information about lighting controllers and vision systems, contact GlobalAutoID for a consultation @ GlobalAutoID.com/contact.
Visit GlobalAutoID.com for more from our Solutions Partners, as well as feature articles on vision, inspection, and automation solutions for the automotive, aerospace, electronics, medical, and consumer packaging industries.
Follow Global Automation & Identification Group on Twitter @GlobalAutoID, and connect with us on LinkedIn.
The audiocast background music is Funkorama by Kevin MacLeod.
Link: https://incompetech.filmmusic.io/song/3788-funkorama
License: http://creativecommons.org/licenses/by/4.0/
The audiocast was recorded and produced by James D Kirk for Global Automation & Identification Group.